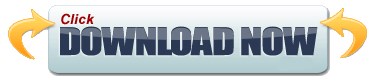
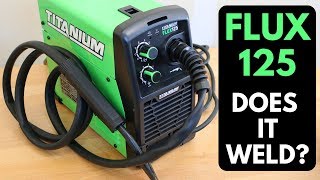
Continue to increase the tension until you’re one-half turn past wire slippage. Loosen the drive rolls, then increase the tension while feeding the wire into a block of wood or metal.
#Speedway series 125 amp flux welder manual pro#
It’s not an exact science, but here are some pro tips to help you get close: Too much tension can cause wear on the wire and too little can lead to birdnesting, so it’s important to find the sweet spot on both parts. Your welding wire not feeding properly off the spool is likely due to incorrect tension on either the spool break, the drive rolls, or both. Once you’re in the habit, it will save you time and money in the long run. You’ll also need to either blow out or replace your liner (more on that later.) Maintaining your wire in between jobs is as easy as taking it out of the welder and putting it under a blanket or in a garbage bag. If you do see rust, you can try and unspool until you find clean wire. Moisture or disuse for long periods of time can cause rust, which in turn will clog up your liner. Here’s where to start.įirst, take a look at the wire itself.
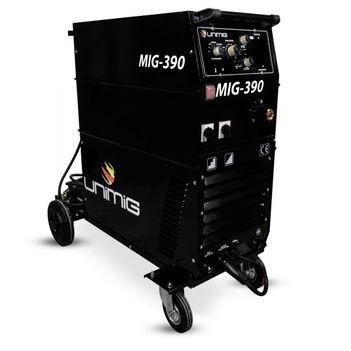
And because wire-feed issues can happen anywhere along the length of the gun, you may need to check several areas until you find the problem. Trouble with your MIG wire not feeding properly can lead to a variety of frustrating problems that lead to downtime, extra cost, and all the associated headaches that come with having to stop what you’re doing and troubleshoot.
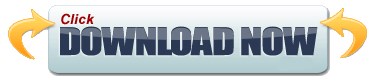